As the manufacturing sector moves into Industry 4.0 and even beyond that into Industry 5.0, the demand for real time operational decision-making means more and more information is being processed at the edge rather than in the cloud. Our technology delivers a complete real-time hypervisor solution, allowing you to process data at the edge in any application where functional safety and cybersecurity cannot be compromised.
Trend
In the past, PLCs were controlled by small microcontrollers. They took over sensor data acquisition, simple but safety-relevant control of actuators and therefore had to meet the corresponding industry standards of functional safety.
In the meantime, high-end devices among PLCs have developed into industrial computers. In addition to old programming standards such as IEC 61131, they can now be programmed with more complex software languages such as C, C++, C# and Visual Basic. In modern networks, they are now active information processors, so-called edge nodes. They include OPC UA server functions and software support for the latest industrial network protocols, for example Time-Sensitive Networking (TSN), EtherCAT or CC-Link IE.
Today many new functions are provided via software instead hardware. But a PLC can only process such a large number of sensors with a higher signal resolution, actuators and robots simultaneously through significantly higher CPU performance.
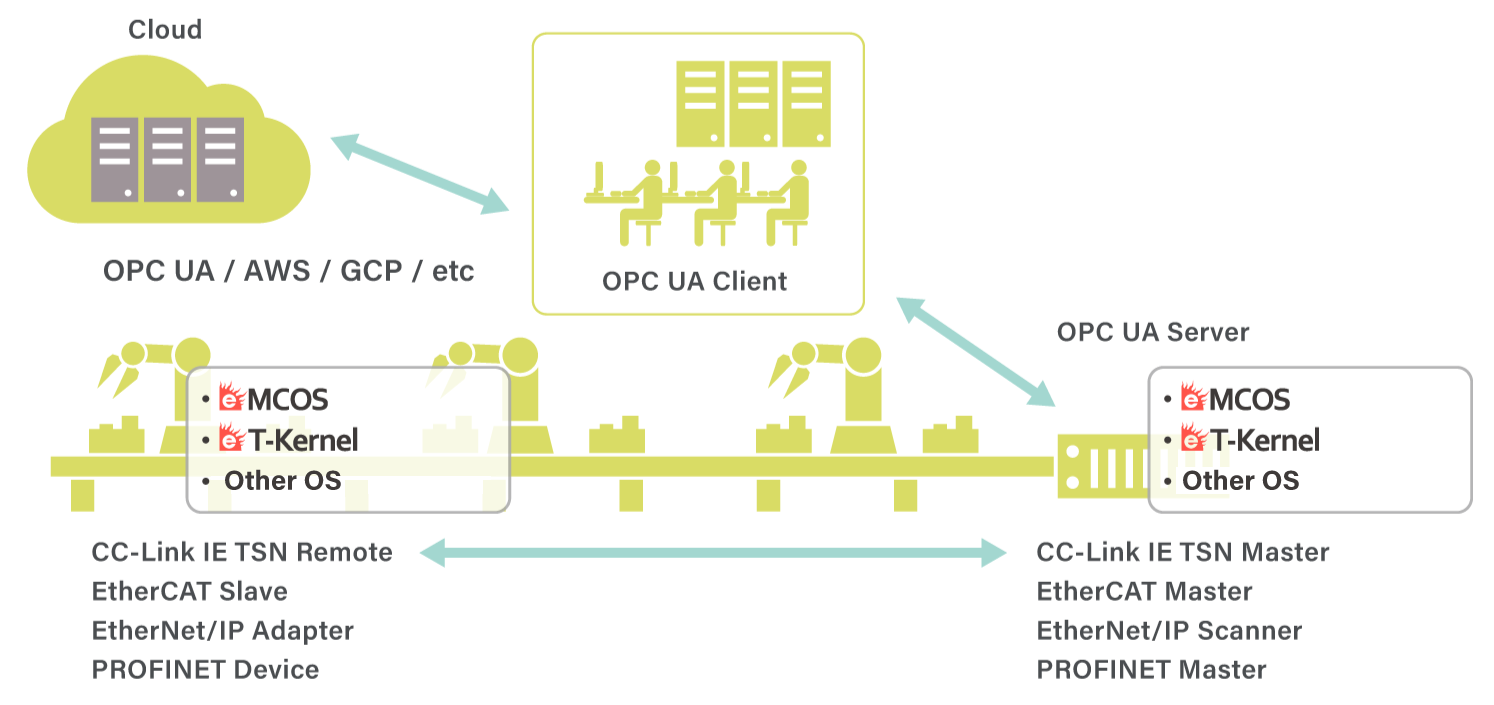
In parallel, the requirements for functional safety to protect human life, the environment and machinery have also increased. To meet these efficiently, new software strategies such as hypervisors are being used.
For example, high-end PLCs come with convenient programming displays. However, for HMI functions, developers use extensive libraries that are not part of the safety concept but run on the same hardware. This HMI function only changes the system function in programming mode, not in operating mode. To meet functional safety requirements, this HMI software is executed in a specially isolated memory area. So-called real-time hypervisors are available for addressing this mixed-criticality purpose.
In traditional IoT systems, most of the data collected by IoT devices is sent to the cloud over the Internet and then aggregated and processed in the cloud (cloud computing). In edge computing, the IoT devices at the “edge of the network” and near the user (edge devices) process and manage the collected data on their own and send only the required data for cloud processing. As shown in Figure 2 below, edge computing also uses a distributed system architecture to process data locally in a distributed manner rather than just centrally.
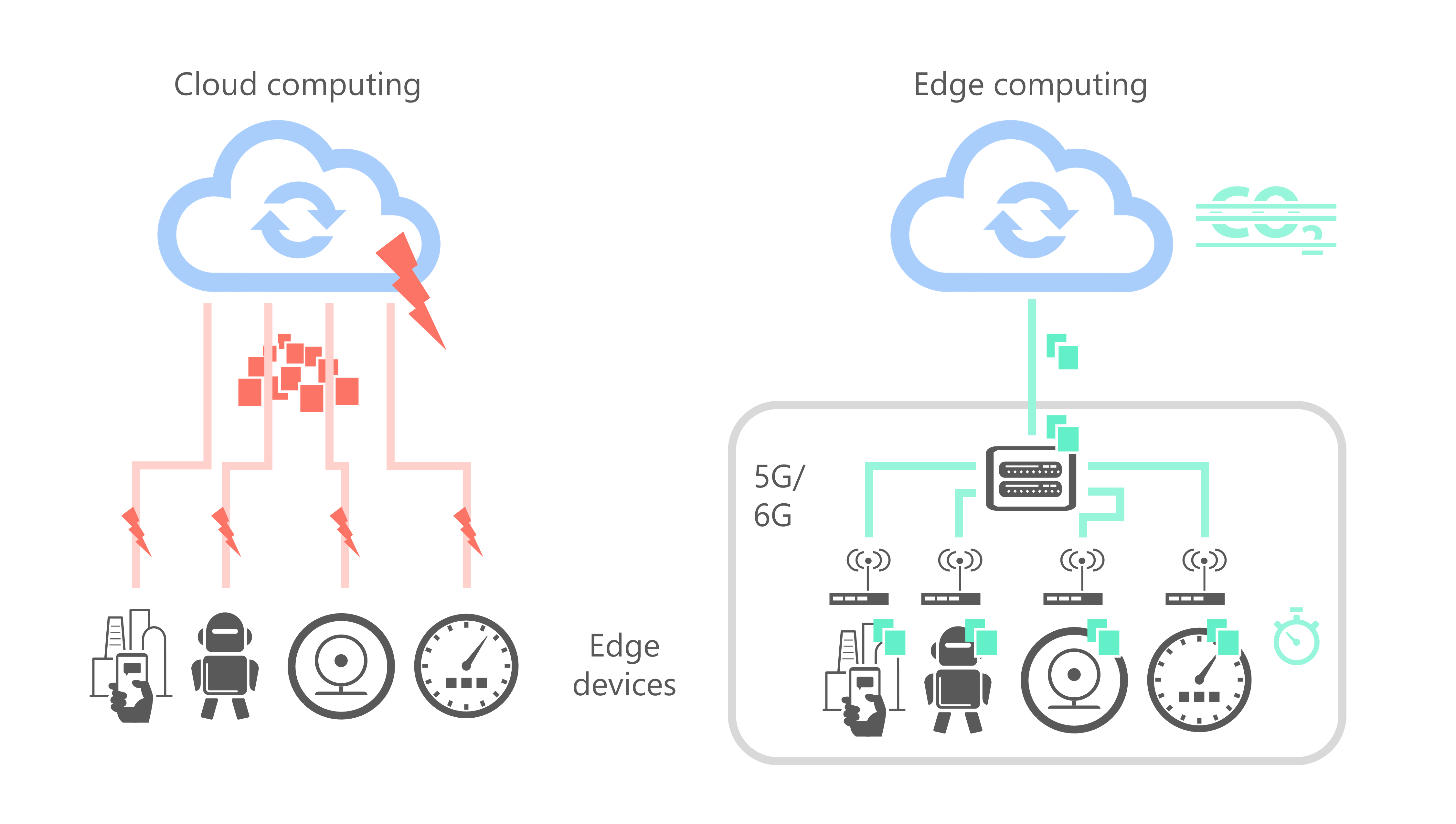
More than 70% of all IoT applications involving industrial automation will rely upon RTOS by 2025 (Mind Commerce, 2020).
In this RTOS world, low-latency communication and deterministic decision-making are the top priorities. By connecting the formerly largely isolated RTOS world with the cloud, security of networks and services to protect users and data from cyberattacks are now added – the attack surfaces of edge devices were dramatically increased by connection to the internet.
Challenges
The demand for edge computing
A variety of edge devices in industrial equipment are becoming increasingly intelligent and so is their data processing. In these intelligent systems, in addition to the real-time performance and low power consumption required by traditional embedded systems, it is essential to process large quantities of data at the edge, which used to be done in the cloud, and to ensure low latency and security when processing data at the edge.
Edge computing therefore requires High Performance Computing (HPC). The advanced data processing that used to take place in the cloud must now take place at the edge of the network, which requires sophisticated and powerful hardware.
Multi/manycore hardware
To achieve high performance, tens to hundreds of processors can be implemented as a single piece of hardware, with operations are executed in parallel on many of these processors simultaneously. The best way to achieve high performance and energy efficiency is heterogeneous multi-many core computing, where multi-many core technology is combined with different processor architectures.
Multi/manycore software
Looking at heterogeneous computing from a software perspective, a traditional single microkernel operating system architecture designed for the single-core era cannot handle different processor architectures in an integrated manner and thus cannot deliver the required performance. To realize highly efficient HPC with heterogeneous multi-many-core computing, an operating system with a modern multikernel architecture (distributed microkernel) is required, where the operating system itself has high parallelism and each processor has its own independent microkernel optimized for heterogeneous computing.
eSOL solution
With eSOL’s new eMCOS® RTOS Platform, Industry 4.0 can be realized securely, meeting edge computing requirements such as highly efficient true parallel processing and complete separation of mixed-criticality applications, while ensuring real-time performance and security.
The advantages of using eMCOS for edge computing are:
- High throughput due to the excellent real-time performance and high parallelism of the operating system itself
- POSIX-compliant multiprocess environment that resembles a general-purpose operating system and allows reuse of already available general-purpose operating system (e.g. Linux) source code
- Real-time hypervisor to re-use source code within a mixed critical system
- Ready-to-use platform support such as ROS, Autoware and AUTOSAR
- High scalability due to multikernel architecture (distributed microkernel)
- High reliability and functional safety as anomalies in the kernel of one core do not propagate to the kernels of the other cores
Learn more